Why Mobile Robots with Lower Payloads are the New Competitive Strategy in Manufacturing Automation
Redefining the Value of Mobile Robots in Autonomous Material Handling
Material handling automation has traditionally emphasized payload capacity, with the value of a given solution based mainly on the amount of weight it can move. This focus stemmed from practical past constraints: human operators with carts or forklifts could only make so many trips per day, so the apparent solution was to maximize the payload transported by each trip.
This mindset, and the common practice of batch-oriented production, led many facilities to apply the same logic when selecting autonomous mobile robots (AMRs) – focusing on heavy-scale machines able to haul substantial pallet loads of 200-600kg (450-1300lbs).
However, the volatile environment of modern manufacturing could now be changing the way automation effectiveness is measured.
Today, competitive advantage belongs to those facilities best equipped to pivot their production workflows at any moment’s notice – rapid pivoting in production adjustment has shifted from facilities that viewed heaviest load capacity as the primary indicator of AMR efficiency.
Instead, the facilities best equipped for rapid production adjustment are now taking the lead. And when prioritizing agility – the larger, heavier AMR solutions no longer provide the greatest value.
Decision Velocity: The Modern Metric for Competitive Advantage
Success of manufacturing operations is often tracked with metrics like throughput, cycle time, and efficiency. But the need to adapt quickly introduces another key factor: decision velocity – the speed at which an organization can spot changing conditions, decide on a response, and execute that change in production.
This capability is increasingly important due to several modern market pressures:
- Shorter Product Cycles: timelines have shrunk from years to months, demanding faster pivots.
- Unpredictable Supply Chains: disruptions require rapid adjustment in material and resource flow.
- Higher Customer Expectation: driving the need for flexible customization and responsive speed.
Consequently, the strategic advantage point has shifted. While efficiency remains essential, there is now greater competitive value in production flexibility than just high production volume alone.
Facilities prioritizing decision velocity gain significant competitive benefits:
- First-Mover Gains: Capitalizing on new trends or demands ahead of the competition.
- Margin Growth: Quickly aligning production with the most profitable opportunities.
- Operational Resilience: Navigating supply chain issues by rapidly adjusting processes.
Recognizing the value of decision velocity reframes material handling investment. It makes on-demand material flow and just-in-time (JIT) resource allocation a strategic imperative – positioning those mobile robots that have the greatest agility and adaptation capabilities as the ideal tools for market leadership.
Agility and Adaptability: Why Compact Mobile Robots Excel
Decision velocity requires a different set of capabilities. Lightweight, adaptable AMRs are specifically designed to suit this approach, with responsiveness and flexibility benefits that larger systems often don’t match:
- Just-in-Time Delivery: Smaller AMRs allow precise, on-demand delivery of materials when and where they’re needed. This minimizes work-in-process (WIP) inventory and allows production to respond quickly to changing demands.
- Rapid Deployment: Lightweight mobile robots can be operational in days, or even hours – integrating into existing workflows with minimal downtime and disruption.
- Lower Adoption Barriers: Designed for associates of all skill levels, these AMRs often have intuitive interfaces – with faster adoption, reduced training time, and minimized human error potential.
- Navigational Flexibility: Compact AMRs can navigate spaces as tight as 3ft wide – operating safely alongside personnel and entering areas that larger systems physically cannot fit.
This emphasis on agility is more than an operational upgrade; it evolves the role of material handling from simply a logistical necessity into a core component of strategic positioning and competitiveness.
Ultimately, strategic value in today’s manufacturing environment is measured not by maximum production capacity, but by the efficiency of your facility material flow, dictating the ability of your production lines to survive changing market demands.
Redefining Manufacturing Workflows: From Batch to Flow
While batch-oriented workflows provide efficiency in stable environments, today’s need for responsiveness highlights its drawbacks. Sticking to batch orientation now creates bottlenecks and limitations that run counter to the goals of agility and rapid adaptation:
- Slow Response Time: Batch schedules are inflexible and difficult to change quickly, delaying responses to urgent orders or supply issues.
- Wasted Floor Space: Significant space is often consumed by staging materials and work-in-process (WIP) inventory required for large batches.
- Inventory Cost: Significant capital remains locked into WIP inventory, increasing carrying costs and financial risk.
- Quality Risk: Defects or quality problems discovered late can compromise entire batches, resulting in waste and higher scrap rate.
- Reduced Visibility: Insight into production status and material location is updated intermittently, hindering proactive management.
Addressing these constraints requires manufacturers to fundamentally re-evaluate their material handling infrastructure in favor of more dynamic systems.
Continuous Production Flow with the Model C2 Autonomous Cart
Breaking from batch scheduling hinges on implementing an automation system that empower pull-based operations. Smaller AMRs like the Model C2, an autonomous delivery cart, offer a solution specifically engineered for this role. Instead of moving heavy pallets, these unintrusive AMR robots excel at frequent, targeted deliveries of items on-demand to their points of need.
“For us, the key was realizing these autonomous carts weren’t just smaller versions of our pallet-moving robots,“ explains a manufacturing technology director. “They enable an entirely different approach to production.“
The Model C2 delivers just-in-time material flow with fully autonomous transport, even within congested areas, around tight corners, and through narrow 3ft passages. Live route calculation and dynamic obstacle avoidance ensure reliable delivery without the need for external facility markers or installations. The cart’s 45-min deployment and no-training usability allow flow-based material handling to be implemented and scaled without production downtime.
This responsiveness allow Model C2 fleets to support facility transitions to ‘pull’ production models – away from constrained batch schedules, and towards actual-consumption alignment.
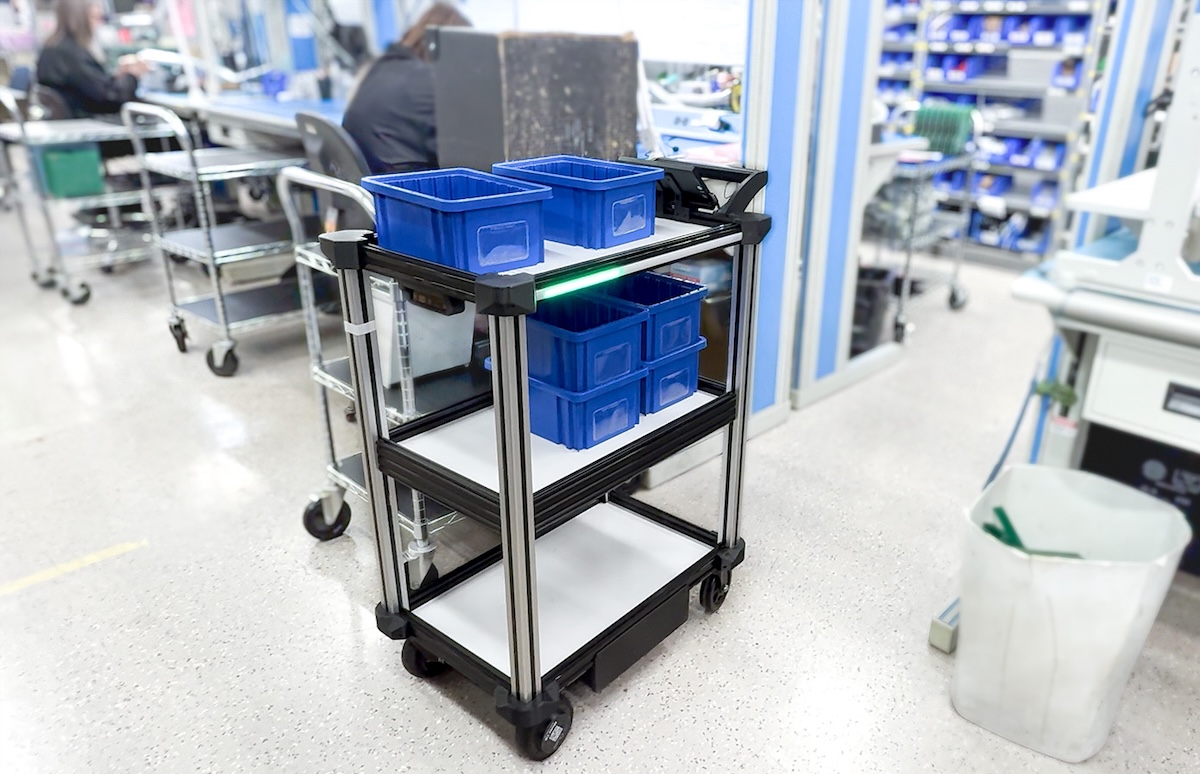
Counterintuitive Efficiency: More Frequent Deliveries on Lighter Mobile Robots
At first thought, replacing one large delivery with multiple smaller ones may seem inefficient. But the benefit becomes apparent when analyzing the impact on total production performance. For example, compare these workflows:
Traditional Batch Delivery Process:
On-Demand Continuous Flow Process:
Single heavy-payload AMR delivers materials twice per shift, every 4-6 hours.
Fleet of nimble C2s provide targeted deliveries every 30-45 minutes
Each station needs 120 sq ft of staging space for materials
Material staging space can be reduced to 15 sq ft per station
Production changes require at least half-day notice & emptying and restocking large inventory areas
Production priorities can change within 1 hour & materials are presented just-in-time at the exact point of use whenever needed
Workers spend up to 12% of their time managing and searching through material inventory
Material search time reduced to less than 1% of worker time, speeding up production turnaround
Through the lens of Lean manufacturing it becomes more clear why frequent, on-demand deliveries are more effective than batch movement. The continuous flow model allows facilities to achieve:
- Minimized Inventory Waste: Just-in-time flow drastically cuts down on excess WIP and associated costs.
- Optimized Space Utilization: Reclaiming floor space previously dedicated to large batch staging.
- Reduced Waiting Time: Materials arrive precisely when needed, preventing workstation downtime.
- Eliminated Motion Waste: Workers focus on value-added tasks as material searching is minimized.
- Increased Production Agility: Faster response to demand shifts and reduced changeover times.
Optimizing material flow across the entire production system unlocks greater strategic value than simply maximizing the capacity of individual transport units.
Validating the Shift: KPIs for Measuring Operational Agility
Evaluating the success of shifting to continuous flow involves measuring progress towards decision velocity and manufacturing agility goals. Subsequent choice of Key Performance Indicators (KPIs) should reflect these objectives:
- Responsiveness: Directly quantify reaction ability using metrics like:
- Changeover Time Reduction (%)
- Time to Implement Schedule Change (Hours/Days)
- Order Lead Time Variance
- Flow Efficiency: Measure system smoothness with KPIs such as:
- WIP Inventory Levels (Units or $)
- Manufacturing Cycle Time
- Ratio of Value-Added Time to Total Lead Time
- Resource Optimization: Indicate efficient asset use through:
- Floor Space Utilization (%)
- Production Output per Square Foot
- Reduction (%) in Labor Hours Spent on Material Handling
Positive trends in these metrics confirm that the transition is leading the organization toward the intended strategic advantages – including better resilience and faster response capabilities.
The Role of ROI in Proving Material Handling Strategy
Calculating ROI based on these strategic improvements serves to validate the investment in agile material handling systems. The ROI measure isn’t just for operational cost savings in this case – it also confirms leadership decision to prioritize agility over traditional metrics.
When manufacturing leaders select automation systems, they reveal more about their strategic vision than they may realize. The choice between high-capacity AMRs and lighter, more adaptable systems is a declaration of how the company chooses to compete in the future, not just a matter of technical preference.
By aligning both Key Performance Indicators (KPIs) and ROI calculations with objectives like improving decision velocity, manufacturers demonstrate how this shift to nimble automation directly impacts their overall competitive advantage.
In Conclusion: The Agility of Mobile Robot Automation Now Defines Competitive Ability
Adapting to volatile markets and evolving customer demands is the defining challenge for modern manufacturing. Success no longer hinges on maximizing payload, but on the capacity for rapid adaptation and operational agility. Achieving this requires embracing “decision velocity” and moving beyond the limitations of rigid, batch-oriented workflows.
Smaller autonomous mobile robots (AMRs), such as the Model C2 delivery cart, are proving highly effective for implementing the just-in-time material flow essential in today’s dynamic manufacturing environments. Unlike traditional heavy-payload systems often tied to rigid processes, nimble solutions like the C2 support true operational flexibility. Features like rapid deployment, minimal space needs, and safe operation alongside personnel allow facilities to adapt quickly without major disruption. This capability enhances the responsiveness and resilience needed to navigate market volatility effectively.
For manufacturing leaders evaluating their automation strategy, the key question remains: Will your material handling system enable adaptation to the next market shift, or will it hinder progress?
To explore how the Model C2 can support more agile operations, visit: www.quasi.ai/c2-cart
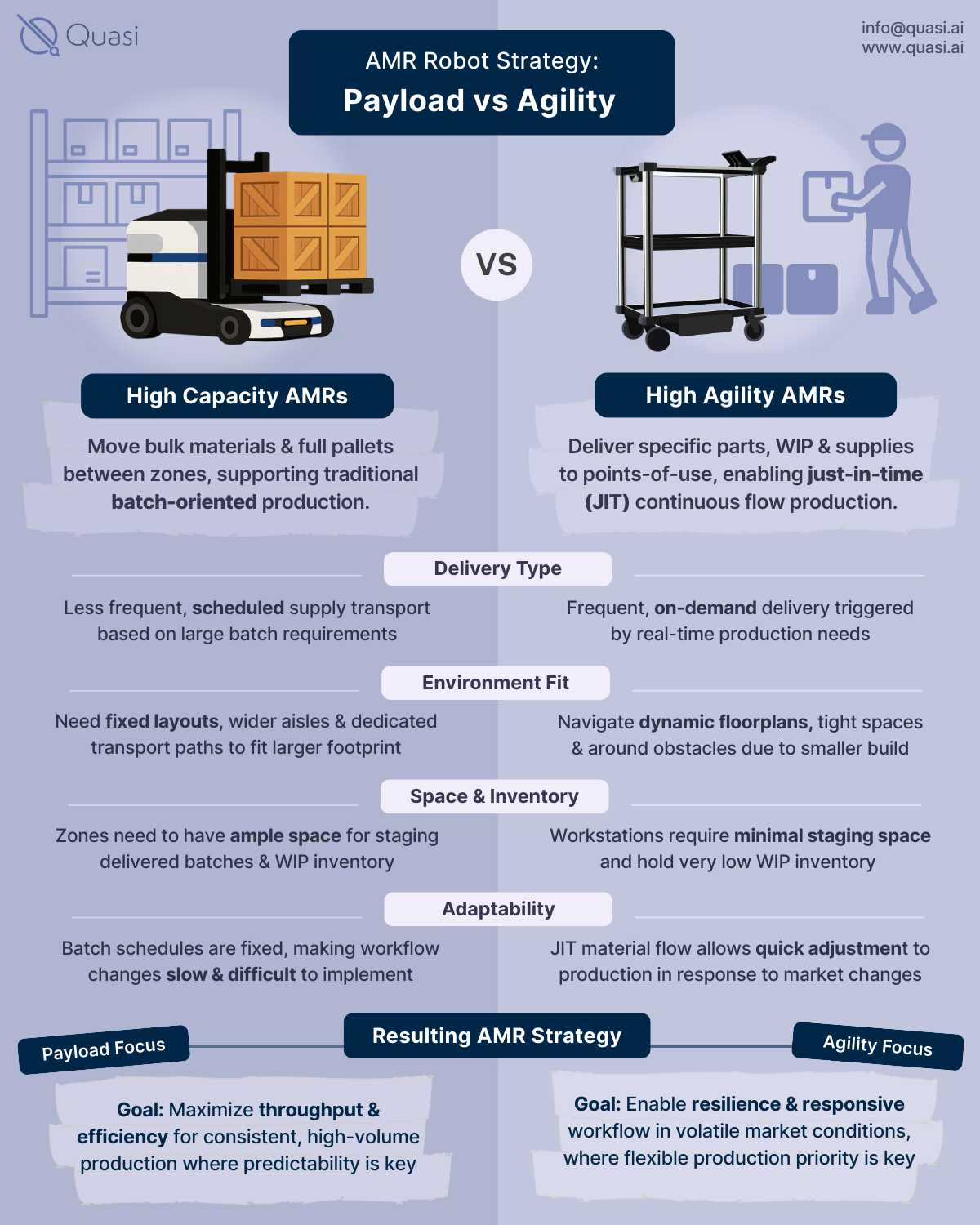