Across sectors like healthcare, manufacturing, and life sciences, the burden of repetitive tasks can drain resources and impact productivity. Autonomous Mobile Robots (AMRs) tackle this problem directly, optimizing complex workflows while keeping costs in check. Armed with adaptive AI and machine learning, AMRs aren’t confined to rigid tasks – they enhance safety, cut errors, and bring an extra layer of intelligence to the workplace.
This article explores the different types of mobile robots in industries today and discusses their ability to go beyond simple automation, optimizing workflows and creating opportunities for innovation.
Table of Contents
2.
AMR Automation:
Automated Mobile Robots (AMRs)
What is an AMR Robot
Autonomous Mobile Robots, shortened to “AMRs”, are a subset of mobility robots that are able map, route, plan, and traverse their environments without assistance from humans or external guides. Instead, AMRs rely on their embedded software, advanced sensors, and artificial intelligence to accurately perceive surroundings, avoid dynamic obstacles, and complete deliveries safely.
LiDAR Sensors
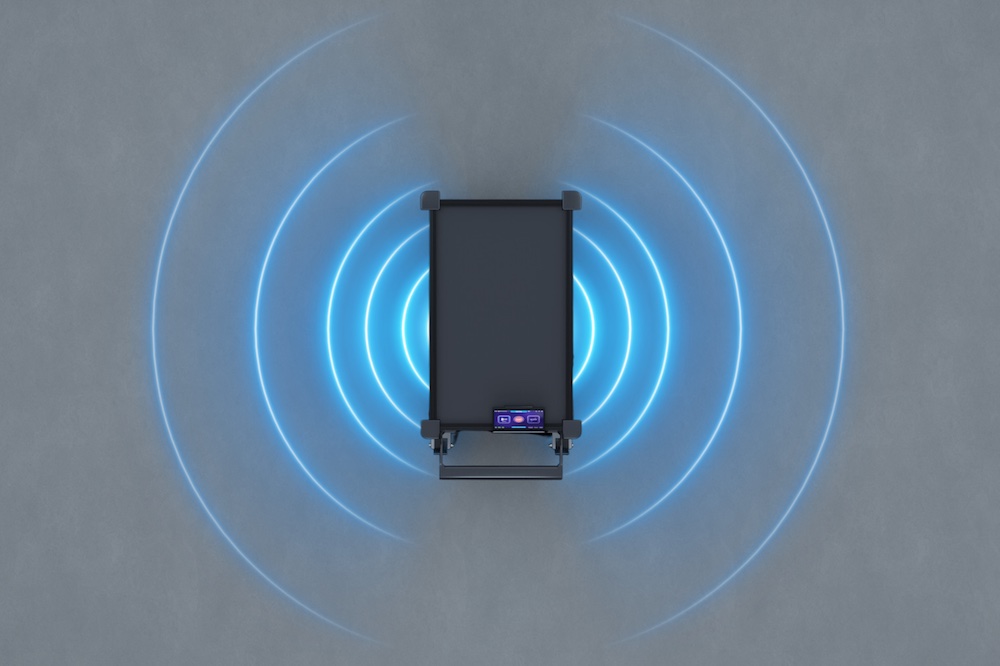
An essential navigational component for AMR robots is Light Detection and Ranging (LiDAR) technology, in the form of an intelligent, 360-degree scanner, located on-board the machine.
The LiDAR scanner sends out beams of light at objects around the AMR robot. As they hit surrounding items, each beam is reflected back to the scanner, where sensors record its travel time and plot the value on an internal map, creating a detailed representation of the robot’s surroundings. This map is updated continuously during the AMR’s operation, serving as a crucial feature for navigation and obstacle avoidance.
Time-of-Flight Sensors
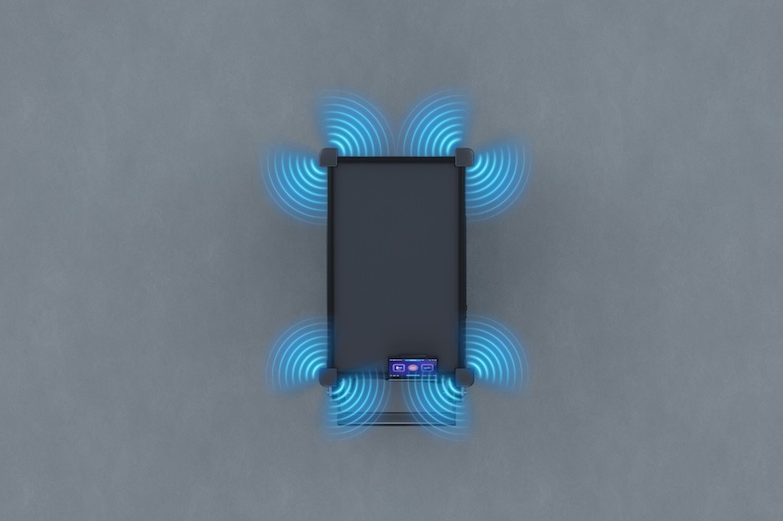
Time-of-Flight (ToF) sensors along the perimeter of the machine body further boost LiDAR’s perception and obstacle-detection abilities. ToFs also emit light signals and measure their reflection times from surrounding objects. However, unlike LiDAR, their perception range is much shorter, allowing them to provide rapid feedback for sudden, up-close changes, so that the AMR can respond accordingly.
By handling close-proximity detection, ToF sensors reduce the processing load on the LiDAR system, which focuses on detailed environmental mapping and long-range route planning. Together, these sensor systems create a comprehensive and responsive navigation system for the AMR.
Other Technology
AMRs may also use additional technologies to enhance their functionality, such as:
- Vision systems: Depth cameras for even greater visual understanding of the environment.
- Ultrasonic sensors: Detect objects using sound waves for increased obstacle detection.
- Inertial Measurement Units (IMUs): Track robot orientation to improve position sensing.
- Bump sensors: Detect physical contact with objects.
Artificial Intelligence and Machine Learning
AMRs constantly interpret data from various sensors – a complex process that had been impossible prior to groundbreaking recent advances in Artificial Intelligence (AI) and Machine Learning (ML). Since mobile robots operate in dynamic spaces shared with humans and other machines, they must process inputs from their own sensors, while simultaneous communicating with external systems and devices.
AI and ML facilitate this level of integration, allowing autonomous robots to do more than automate simple tasks. They can intelligently respond to their surroundings, optimize routes, avoid obstacles, and continuously learn for improved efficiency and safety.
AMRs vs AGVs
With the advent of mobility in different types of robots, differentiating between terminology and features has become increasingly difficult. In the case of Autonomous Guided Vehicles (AGVs), their similar appearance to AMRs creates an additional point of confusion.
But though AGVs possess mobility skills, and even some level of sovereignty, they’re better thought of as the less-intelligent predecessors to today’s modern Autonomous Mobile Robots (AMRs) when comparing degrees of autonomy:
AGVs: Guided Autonomy
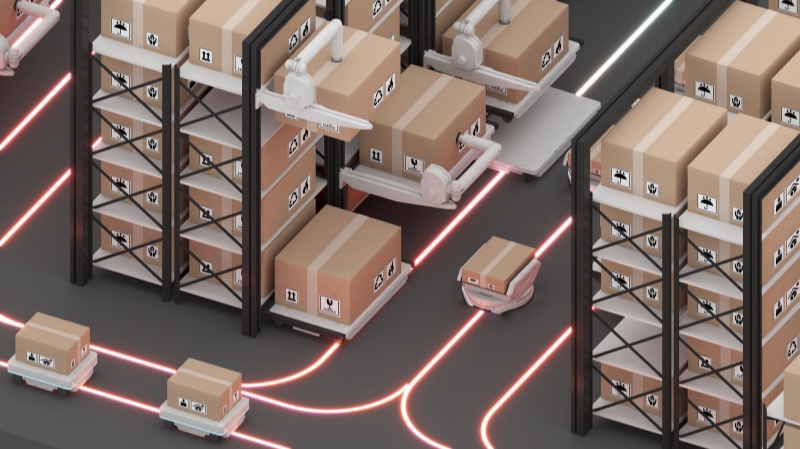
As their name suggests, AGVs require external information to self-navigate. They rely on facility modifications – lanes made from reflective tape, magnetic markers on the floor, signals from overhead wires, and so on – to guide them along their paths.
AGVs are “autonomous” in the sense that they don’t need human assistance to travel along these predefined routes, so long as the guidance markers are there, visible, and accurate between each waypoint. Many AGVs are also equipped with basic obstacle detection, enabling them to stop in the event of sudden interference – another point for their autonomy.
However, this type of autonomy is more about performing repetitive, pre-programmed tasks on their own, rather than independently making navigational decisions.
AMRs: Self-Decided Autonomy
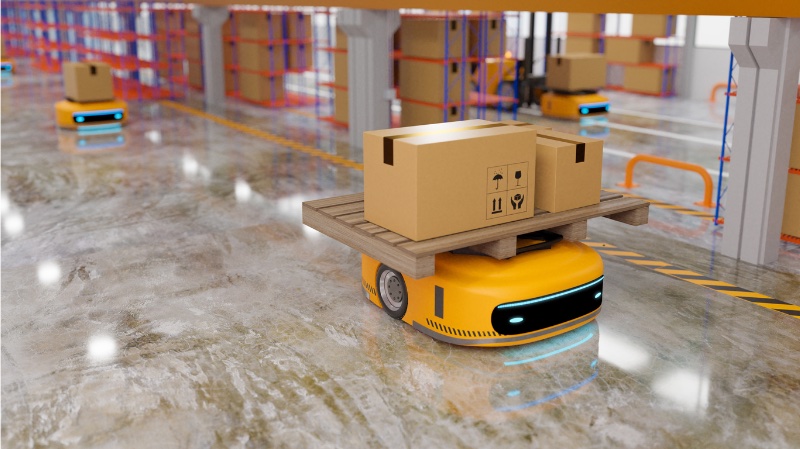
AMRs, on the other hand, rely solely on their embedded technology to understand and adapt to their surroundings, make decisions on optimal routes, and avoid unexpected obstacles. They use more complex sensors, like vision cameras, LiDAR and ToF scanners, along with Artificial Intelligence (AI) and Machine Learning (ML) to learn from encountered situations and become more efficient over time.
The lack of infrastructure modifications also makes AMRs much faster and more cost-effective to deploy. In the case of the Quasi Model C2 autonomous cart, for example, initial deployment takes less than a single hour. In sharp contrast, AGVs take weeks, or even months to set up for use, and the associated cost can range from a few thousand to hundreds of thousands of dollars.
3.
Types of AMR Applications
In-Use Today
Applications of robotic mobility are increasing across many industries. Today, automated mobile robots can be seen transporting supplies and materials, performing disinfecting tasks for facilities, and helping in inventory management efforts for small and large scale operations alike.
Material Handling and Transport AMRs
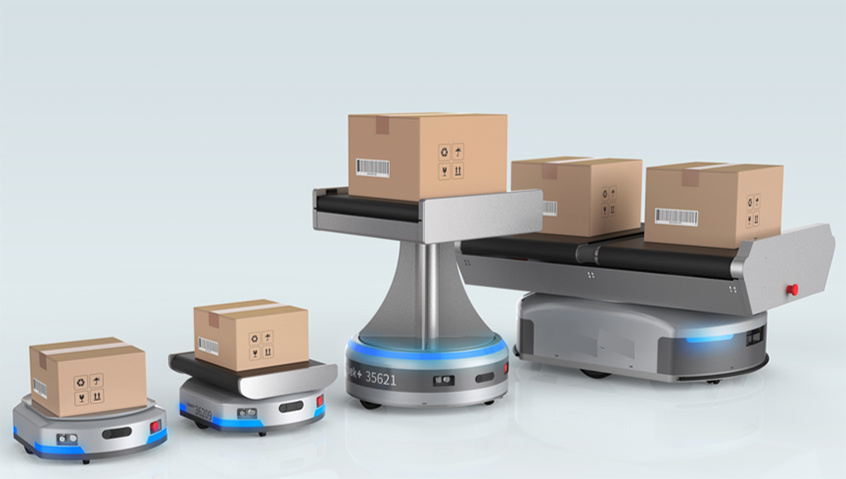
Transport AMRs automate internal material movement in dynamic environments ranging from hospitals to warehouses to laboratories. These types of robotics are more flexible than fixed conveyor systems and more quick and agile than human counterparts. By incorporating AI and ML, they integrate with existing systems and allow for intelligent routing and obstacle avoidance and responsive material handling.
Transport and Movement AMRs include:
- Tugger AMRs: Pull heavy inventory pallets and material carts, between processing zones to delivering items
- Laboratory Transport AMRs: Automate sample, specimen, and equipment movement between workstations within a research workflow
- Medication Delivery AMRs: Transport medications and patient supplies securely within healthcare facilities
- Bin-Carrying AMRs: Transport pick bins to packing/shipping areas in warehouse operations
Cleaning and Sanitization AMRs
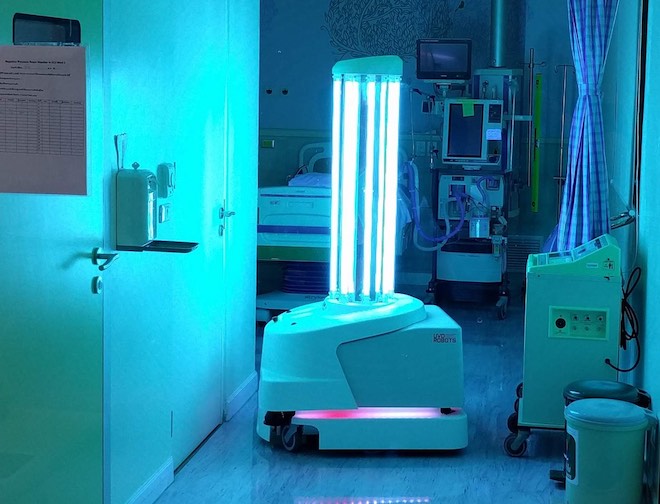
AMRs provide a consistent and dependable option for automating cleaning processes and reducing contamination risk and contagion spread. Designed for environments ranging in complexity from hospitals to offices to crowded public facilities, the mobile robot enhances sanitation upkeep with less variability.
Common Antiseptic AMRs include:
- Floor Cleaning AMRs: Vacuum, scrub, and sweep the surfaces of a mapped facility
- Disinfecting AMRs: Use UV light or chemical sprayers to sanitize surfaces
- Air Filtration AMRs: Capturing airborne contaminants like dust, allergens, and pathogens
- Pool Cleaning AMRs: Navigate underwater to scrub pool surfaces and vacuum debris, maintaining water clarity
Inspection and Surveillance AMRs
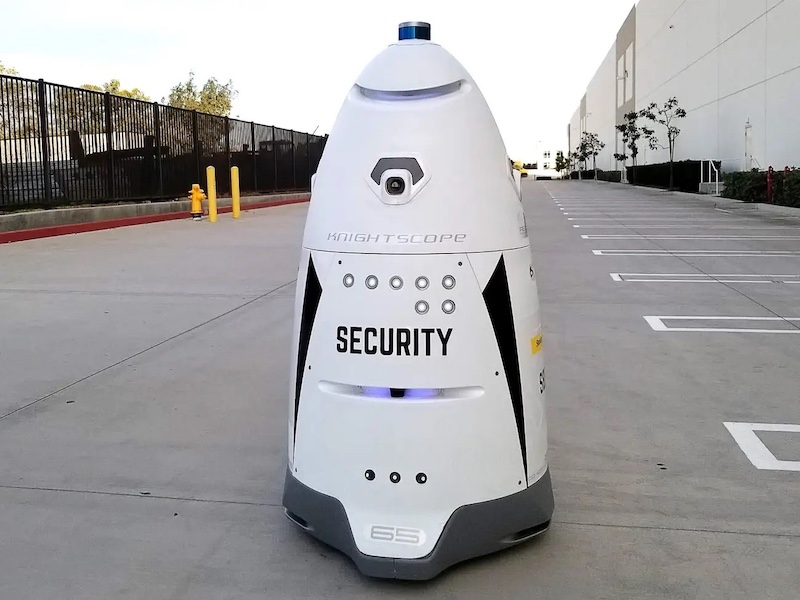
Applications of robotics for public safety provides continuous, autonomous surveillance and security. By supplementing human patrols, these specific robots keep watch 24/7 and integrate with existing policing systems to provide real-time analysis in hard-to-access locations.
Surveillance and Inspection AMRs include:
- Security Patrol AMRs: Patrol public areas like campuses and parking lots, with features like night vision, motion detection, and real-time video streaming
- Facility Inspection AMRs: Inspect machinery, storage, and structure in industrial settings with cameras and thermal imaging sensors to assess conditions
- Crowd Monitoring AMRs: Manage crowds levels via cameras and analytics software to estimate attendance figures, detect flow patterns, and identify safety concerns
- Emergency Response AMRs: Assist first responders during natural and man-made disasters by navigating inaccessible environments too hazardous for humans and providing real-time analysis
Autonomous Handling and Manipulation AMRs
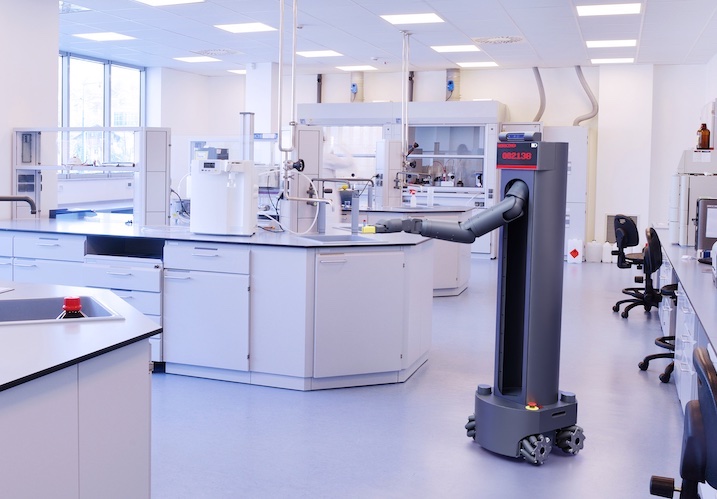
Handling and manipulation AMRs go beyond basic transportation, using articulated arms and specialized end-of-arm tooling to interact physically with their environment. This allows automated execution of more complex and dynamic tasks within warehouses, industrial facilities, and other settings.
Material Handling and Manipulation AMRs include:
- Pick-and-Place AMRs: Locate, grasp, and move individual items for workflow support, order fulfillment, and sorting operations, like the Quasi Robotics Model R2, with dexterity and precision
- Assembly AMRs: Perform the precise placement and connection of components in manufacturing or kitting processes
- Collaborative AMRs (Cobots): Designed to work in tandem with human workers, often providing lifting or maneuvering assistance as part of a workflow
4.
How AMRs Address
Today’s Industry Challenges
Resource managers in industries as diverse as life science, healthcare, manufacturing, and warehousing, often face an equally dismal dilemma; the choice between:
- Incurring additional labor costs for low-level, high-repetition tasks.
- Diverting the focus and expertise of skilled staff in order to handle low-level, high-repetition tasks.
For tedious, intra-logistics tasks — material handling, supply delivery, waste collection, etc. – re-training part-time, hourly help from a pool of high-turnover, low-skill candidates leads to consistently increased labor and training expenses.
On the other hand, relegating experienced team members to these menial tasks, diverts their focus from higher-value responsibilities. It also places the burden of added assignments to an, often already-overburdened team, underutilizing their abilities, decreasing productivity and morale, and increasing human effort as a result of burn out.
Mobility in robotics offers the solution to bridge this gap. By taking on the low-value, time-consuming tasks with incredible reliability, AMRs enable organizations’ employees to engage in higher-value processes. In the long-run, a single upfront investment will enable continued automation and efficiency throughout the facility’s entire operational lifespan such as:
- Optimize Workforce Utilization: When mobile robots take care of repetitive chores, skilled personnel are empowered to apply their expertise (and resulting productivity!) toward higher-value activities.
- Reduce Personnel Costs: Inspect machinery, storage, and structure in industrial settings with cameras and thermal imaging sensors to assess conditions.
- Reduce Personnel Costs: AMR robots represent a single upfront investment, unlike sustained expenses of hiring additional staff. This not only translates to immediate cost savings, but also eliminates ongoing recruiting challenges of temporary workers.
- Improve overall facility safety: AMRs work tirelessly, 24/7, streamlining workflows and reducing bottlenecks. For hospitals, that could mean faster delivery of essential supplies, for production lines, it might yield smoother flow of materials between stations.
Yet, the overall benefits extend even further than immediate productivity gains. By creating a more efficient and dynamic work environment, AMRs foster a culture of innovation and adaptability, allowing organizations to stay ahead of the curve in their respective industries.
5.
AMR Automation
Examples by Industry
Traditional automation often felt like a distant dream for small-to-midsize companies. Today’s reality is that prohibitive upfront investment, complex infrastructure modifications, and intensive personnel retraining are now things of the distant automation past.
Latest tech advances bring automation within reach, even on the SME level, requiring no changes to the facility’s current set up, a minimized initial investment, and no disruption to employee process flows. This translates to much faster ROI recuperation. Some deployments see their upfront costs repaid within the year or even less, gaining an immediate competitive edge as soon as their mobile robots are unpacked.
Life Science Industry Challenges
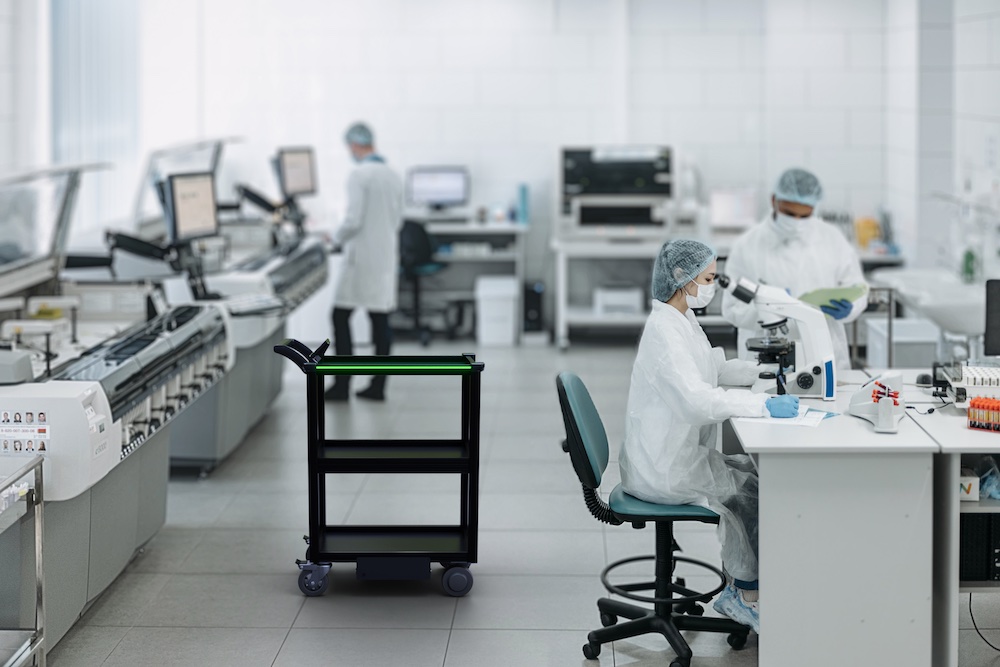
Challenge: Manual Movement of Samples Between Stations
Lab Technicians carry biological samples by hand between processing stages – from collection point, to analysis labs, and then to storage areas. This requires careful handling and maneuvering, which takes up substantial time and is error prone. Often, samples are mixed up and delivered to incorrect stations or are late for processing due to transport delays.
Long-Term Outcomes:
AMR Opportunity:
Deploy a fleet of Autonomous Robotic Carts to transport samples between processing stages.
Challenge: Testing Supply Distribution and Sterilization
Testing staff are required to pick up and drop-off glassware and equipment before and after their testing process. Multiple, hands-full trips are often needed between the autoclave and research station, which can delay experiment start-times and prevent following groups from being admitted to the lab.
Long-Term Outcomes:
AMR Opportunity:
Implement an AMR solution to distribute clean equipment and glassware to each station. Post-session, it will also collect soiled items for sterilization and remove waste from each station.
Healthcare and Hospital Industry Challenges
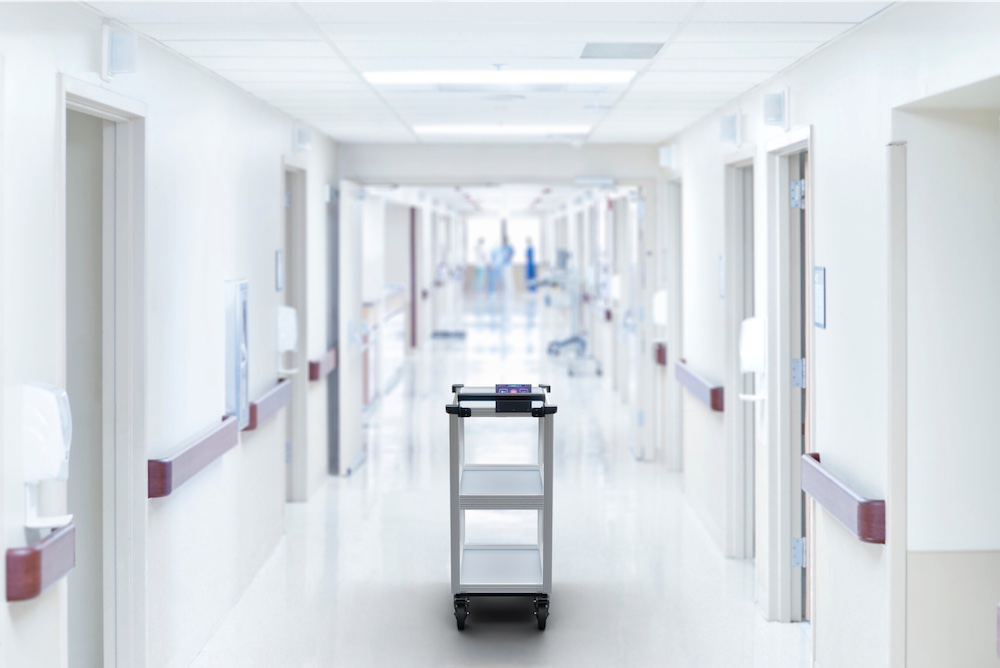
Challenge: Timely and Accurate Medication Delivery
Hospital staff manually deliver medications on foot from the pharmacy to wards and patient rooms, navigating complex layouts and requiring meticulous attention to detail to avoid errors. This is labor-intensive, inefficient, and potentially risky. In large facilities, long distances and wait times exacerbate these challenges.
Long-Term Outcomes:
AMR Opportunity:
Implement an AMR solution to distribute clean equipment and glassware to each station. Post-session, it will also collect soiled items for sterilization and remove waste from each station.
Challenge: Patient Documentation Transport
Patient records, documents, and test results are moved manually between diagnostics, patient rooms, and specialists is done via staff hand-off. This requires nurses and runners to spend time transporting documents securely to ensure confidentiality and compliance with healthcare regulations. Receipt of documents is prone to delays, misplacement, or breaches in patient confidentiality, impacting the efficiency of patient care and hospital operations.
Long-Term Outcomes:
AMR Opportunity:
Deploy Autonomous Mobile Robots equipped with secure compartments for the transport of patient records and documentation throughout the hospital.
Manufacturing Industry Challenges
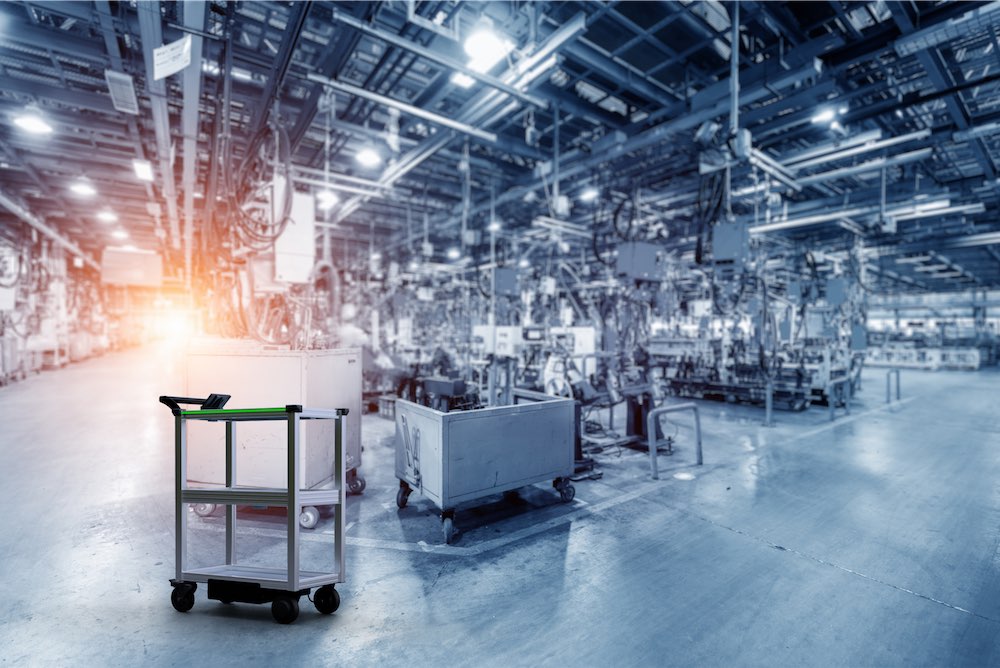
Challenge: Tool and Equipment Distribution
In a production facility, tools and equipment are transported manually from a central storage location and then must be shared between production lines and employee stations. Attempts to distribute and share these resources “as-needed” have resulted in delays and downtime, lost productivity, and frequent misplacement of items. Recently, departments facing strict deadlines without the proper tools to meet them, have even begun cutting corners on certain manufacturing standards.
Long-Term Outcomes:
AMR Opportunity:
Implement Autonomous Mobile Robots for hourly distribution, collection, and rotation of tools and equipment between workstations and departments.
Warehousing & E-Commerce Industry Challenges
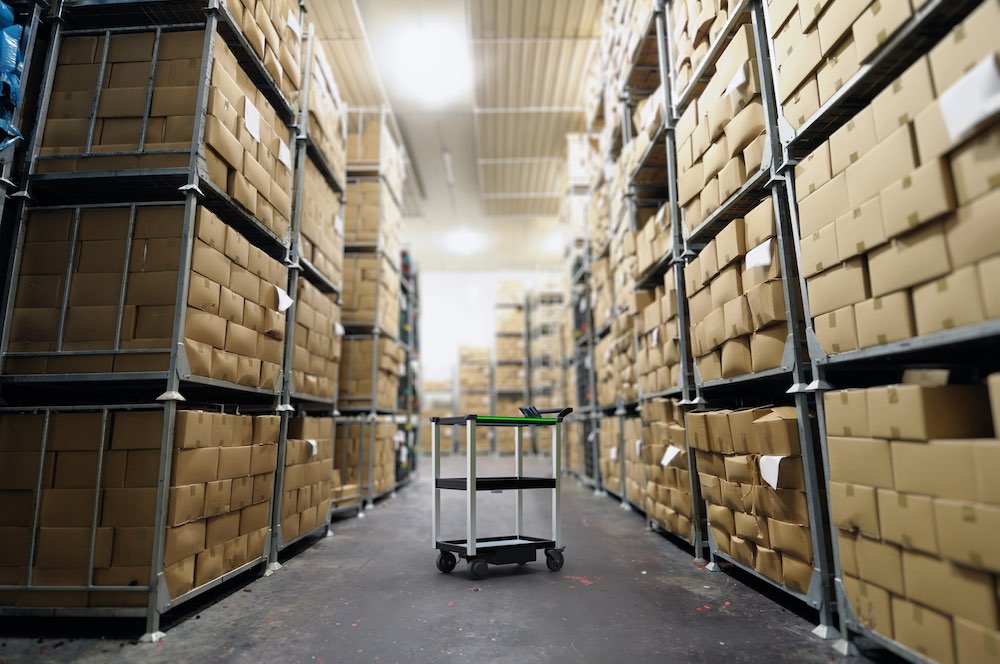
Challenge: Cross-Docking Operations
In warehousing, cross-docking involves incoming goods being directly transferred from receiving docks to outbound shipping docks, with minimal or no storage in between. When completed manually, the process requires precise coordination and timing to ensure that goods are quickly and accurately moved from one dock to another. Otherwise, the facility experiences delays, misrouting of goods, and increased labor costs.
Long-Term Outcomes:
AMR Opportunity:
Implement Autonomous Mobile Robots to streamline cross-docking operations
6.
Conclusion:
While AMRs excel at efficiency and precision, their true impact lies in what they enable for human employees. By taking over mundane and routine tasks, AMRs free up skilled workers to focus on higher-value contributions, problem-solving, and strategic initiatives.
This synergy between humans and intelligent machines isn’t simply about optimization; it’s about fostering a culture of adaptability and continuous improvement within the workplace, preparing teams for whatever challenges the future holds.
To see how companies like Quasi Robotics are pioneering this transformation, explore our real-world AMR solutions today.